To be at the top of the food chain, you need advantages so you can not only survive but thrive in your sector. Today’s sublimation market is increasingly favouring high-volume, high-speed models, which currently make up 75% of the market[1]. Mimaki’s industrial-scale sublimation transfer inkjet printer, the Tiger600-1800TS, seeks to outpace expectations. Designed for companies looking to enhance their competitive edge, this printer delivers industrial productivity, consistent print quality, and cost-effective performance.
An Industrial Tiger
As an industrial textile inkjet printer, the Tiger600-1800TS is designed to handle high-volume textile productions and large projects with ease, without compromising the high standard quality Mimaki’s printers are known for.
Due to its size and high performance, this printer would also make a clever, efficient, and cost-effective choice to replace a production line with multiple smaller printers. It can handle diversified production and applications with a flexible, quick, and high-quality process.
The printer’s ability to handle lightweight paper down to 25gsm enables users to save on paper costs, reducing the total printing cost by up to 40%. Additionally, the Mini Jumbo roll unit allows for larger media rolls up to 300kg, further reducing operational costs and providing per-square-meter advantages over standard rolls.
Outstanding Speed
The Tiger600-1800TS doesn’t share a name with one of the fastest land mammals on the planet for no reason. Thanks to Mimaki’s new-generation printheads, the Tiger600 offers unparalleled speed and productive printing, reaching up to 550 m²/h— a remarkable 143% of the previous model’s speed. Combined with its unique features, the Tiger600-1800TS sets a high benchmark for the future of digital sublimation printing.
Due to the latest attributes, high speed printing can be maintained throughout with minimal intervention needed. A new ink system design helps to reduce the risk of nozzle drop out during operation, including components like an internal buffer tank to automatically replace ink, regular circulation of inks, degassing directly above the printheads to avoid air from entering and flushing boxes on either side to bypass the need for additional colour bars.
It’s also equipped with Mimaki’s quintessential core technologies, including the Nozzle Recovery System (NRS) which allows printing to continue even if a nozzle head is clogged, are also included. Colourama, a company which specialises in fashion, home décor and other digital printing services, remark that they have only needed to replace one printhead for its four Tiger machines over the past four years.
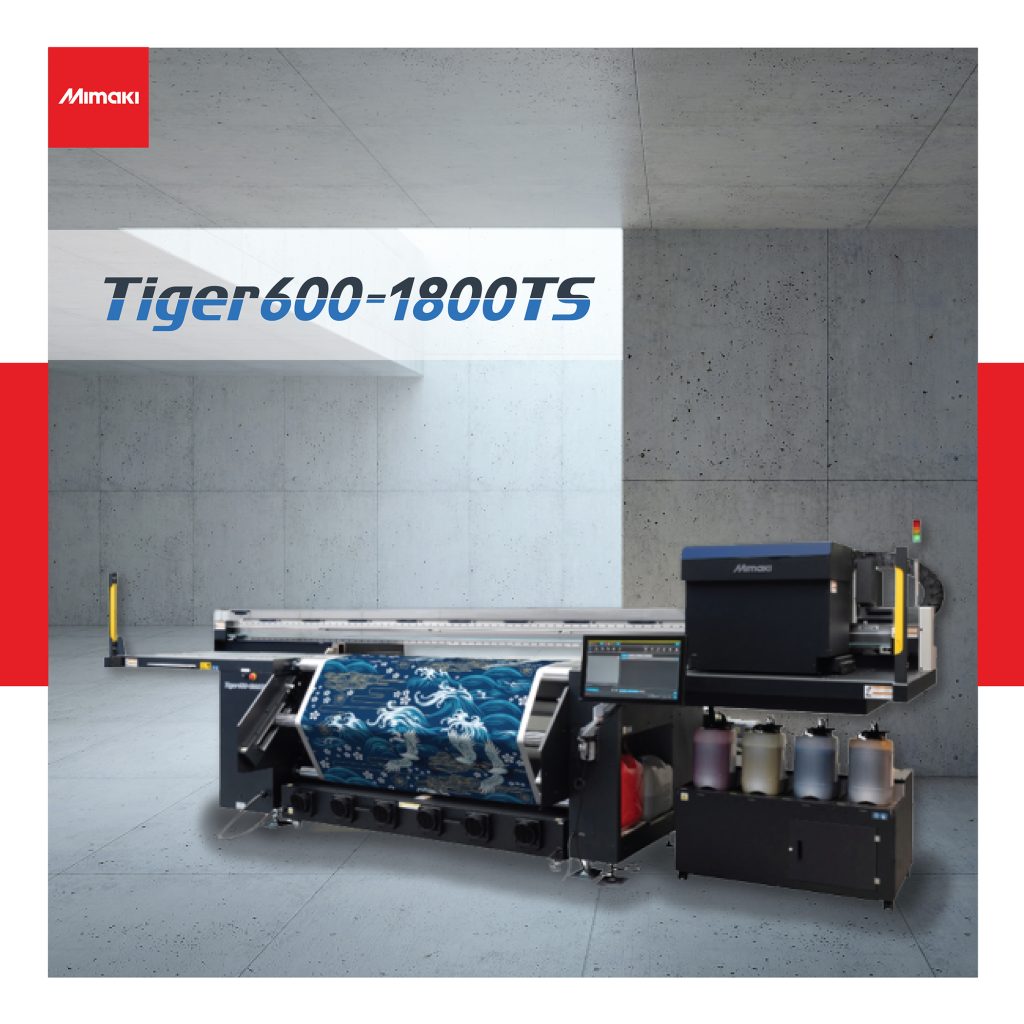
Dye of the Tiger
Not unlike the striking orange and black fur of a tiger, the printer delivers sharp and high-quality prints. Using high density and wide color gamut MLSb510 ink and eight advanced print heads at 240mm per pass, it delivers vivid results with almost no ink satellites, even on high speeds. The Tiger excels in black dye by achieving an extremely deep black colour – arguably the deepest in the market – all in just one printing pass.
The Tiger600-1800TS is also equipped with Mimaki Advanced Pass System (MAPS4) technology, which calculates the best way to inject the ink drops on the varied materials.
As Tiger-user Colourama primarily prints for fashion and home décor, the team is oftentimes tasked with creating colourful and highly detailed pieces. For this reason, the company chose to invest in several Tiger printers due to the vibrant solid colours and sharp details that it can produce, even on high speeds.
Environmentally Conscious
Sustainability has remained one of if not the key issue across all industries for several years now, and the Tiger600-1800TS was created with that in mind.
Compatible with Mimaki’s ECO PASSPORT certified ink, companies can create ecofriendly prints, allowing them to pursue the OEKO-TEX® certification. The printer inks are also bluesign® certified, one of the most stringent eco certifications in the world to certify the highest level of consumer and worker safety, and environmental friendliness.
Improved space-saving design
Both the interior and exterior were considered to ensure that the printer is fully optimised to its environment. All the mentioned features are compacted in a space saving unit, with the paper set up and taken out both at rear of the machine. As it doesn’t need to be accessible from both sides, it takes up 50% less space than the previous Tiger model. The mobile heating unit is situated underneath the machine, allowing for easy paper loading. The 300kg mini jumbo rolls reduce the need for continuously reloading the paper.
For printers considering making the leap to digital textile printing technologies, the Tiger600-1800TS is a highly productive and self-sufficient industrial addition, with built-in capabilities to not only keep up with fluctuating demand but also thrive in a fast-paced environment.